One of the promising areas that many people are now paying attention to is 3D metal printing, the price of which is affordable. Arguing the popularity of this method is quite simple. The fact is that at present it is one of the most promising industries, which will soon be able to replace prototyping options. A big plus is the material that is used to create models. It is possible that in the near future such printers will be located at bases and construction sites, but for now it is worth understanding their types and the principle of operation.
A 3D printer, which produces metal printing according to technologies, can produce almost any figure for which there is a three-dimensional model.
How is the work going?
Nowadays, 3D printing with steel is most often carried out, it occurs due to the fact that both laser and inkjet printers are used. In both cases, the mass is applied layer by layer, thanks to which the desired object will be created. After that, a sufficiently solid model will "grow" on a special platform for building. Selective laser sintering, electron beam melting and deposition inkjet modeling are currently highlighted. Each of these options will be different and are best used in certain industries.
Of course, models that are made of metal, and not of plastic, will be stronger and have more design solutions. In addition, in the future, the created parts can be used in practice without any problems, put into production as a trial version. We can say that 3D printing with titanium or steel can speed up many processes in production, help to avoid a large number of errors.
What will be the price of the product?
Most often, the cost of the model will be based on 3 indicators:
- Options. This includes dimensions and volume.
- The speed of the ordered product.
- The type of metal that is used to make parts, as well as the number of treatments after creation.
Material prices may vary. It is best to check directly with the company, but usually one cubic centimeter of stainless steel costs about 550 rubles. Standard time to create a model can be from 15 days to 1 month.
At the request of the customer, titanium, stainless or carbon steel can be used. Individual alloys are also used, the composition of which is announced to specialists. 3D printing of metal parts is also carried out abroad.
These filaments contain a significant percentage of metal powders, but also enough plastic to print at low temperatures with any 3D printer. At the same time, they contain enough metal to look, feel and have a weight close to that of a metal object.
Products made of filament containing iron even rust under certain conditions, which adds credibility, but they cannot rust through and deteriorate from this - and this is their advantage over real metal objects.
The advantages of such materials:
- Unique appearance printouts
- Ideal for costume jewelry, figurines, household items and decor
- High strength
- Very little shrinkage during cooling
- Heated table optional
- Low product flexibility, depends on print design
- Not considered safe in contact with food
- Requires fine tuning of nozzle temperature and filament feed rate
- Post-processing of products is necessary - grinding, polishing
- Rapid wear of the extruder nozzle - filament with metal is very abrasive compared to conventional materials
3D metal printing in industry
If you are looking to purchase a real metal 3D printer for enterprise use, then there are two pieces of news for you - good and bad.
The good news is that their range is quite wide and continues to expand - it will be possible to choose a device that meets any technical requirement. Further in the article you can see this.
The bad news is the prices. The cost of professional metal-printing printers starts anywhere from $200,000 and goes up indefinitely. In addition, even if you choose and purchase the most inexpensive of them, the purchase of consumables, scheduled maintenance with the replacement of components, and repairs will be a separate blow. We do not forget about the staff and the costs of post-processing products. And at the stage of preparation for printing, you will need special software and people who can handle it.
If you are ready for all these expenses and difficulties - read on, we will present some very interesting samples.
3D metal printing - application
Some industrial sectors already use metal 3D printers, they have become an integral part of the production process, which the average consumer may not be aware of:
The most common example is medical implants and dental crowns, bridges, prostheses, which are already considered the best option for patients. Reason: They can be 3D printed faster and cheaper and tailored to the individual needs of each patient.
The second, equally common example: jewelry. Most major manufacturers are gradually moving away from 3D printed molds and stencils to direct metal 3D printing, and titanium printing allows jewelers to create designs that were previously impossible.
In addition, the aerospace industry is becoming more and more dependent on 3D printed metal products. Ge-AvioAero in Italy is the world's first fully 3D printed factory that produces components for LEAP jet engines.
The next industry using metal 3D printers is the automotive industry. BMW, Audi, FCA are already seriously considering applying the technology to series production, not just prototyping, where they have been using 3D printing for years.
It would seem - why reinvent the wheel? But here, too, 3D metal printing has found application. For several years now, manufacturers of bicycle components and frames have been using 3D printing. Not only in the world, but also in Russia, this has become widespread. Exclusive bike manufacturer Triton is finishing up a project with a 3D printed titanium frame element that reduces weight without compromising strength.
But before metal 3D printing really takes over the world, there are a few major challenges that need to be overcome. First of all, it is the high cost and low speed of production of large series by this method.
3D metal printing - technologies
Much can be said about the use of metal-printing 3D printers. There are specifics, but the main issues are the same as with any other 3D printers: software and hardware limitations, material optimization and multi-material printing. We won't talk about software many, to mention only that the major publishers such as Autodesk, SolidWorks and SolidThinking all develop software products for use in metal 3D printing so that users can bring to life any shape imaginable.
IN Lately examples have emerged that 3D printed metal parts can be as strong as traditionally produced metal components, and in some cases even surpass them. Created using DMLS, the products have the same mechanical properties as those of solid cast counterparts.
Let's look at the available metal 3D printing technologies:
Process #1: Layer by layer powder fusion
The process of 3D printing metals that most major companies use these days is known as powder bed fusion or sintering. This means that a laser or other high-energy beam fuses particles of evenly distributed metal powder into a single whole, creating layers of the product, one after another.
There are eight main manufacturers of metal 3D printers in the world, most of them are located in Germany. Their technologies go under the acronym SLM (Selective Laser Melting) or DMLS (Direct Laser Metal Sintering).
Process #2: Binder Jetting
Another professional method with layer-by-layer bonding is gluing metal particles for subsequent firing in a high-temperature furnace, where the particles are fused under pressure, making up a single metal whole. The print head applies the coupling solution to the powder substrate in layers, as conventional printer on sheets of paper, after which the product is sent to firing.
Another similar but different technology based on FDM printing is mixing metal powder into metal paste. Using pneumatic extrusion, the 3D printer extrudes it, much like a 3D construction printer does with cement, to form 3D objects. After the desired shape is printed, the objects are also sintered in an oven. This technology is used by Mini Metal Maker - perhaps the only more or less affordable metal 3D printer ($1600). Add the cost of a small kiln.
Process #3: Welding
You might think that among the metal printing technologies there is no similar to the usual FDM, however, this is not entirely true. You can't melt metal filament in the hot end of your 3D printer, but major manufacturers own this technology and use it. There are two main ways to print with solid metal material.
One of them is called DED (Directed Energy Deposition), or laser cladding. It uses a laser beam to fuse metal powder that is slowly released and deposited from an extruder, forming layers of an object with an industrial arm.
Usually this is done inside a closed chamber, however, with MX3D as an example, we see the possibility of implementing a similar technology in the construction of a real full-sized bridge, which is due to be printed in 2017 in Amsterdam.
The other is called EBM (Electron Beam Manufacturing), a technology for forming layers of metal raw materials under the influence of a powerful electron beam, with its help create large and very large structures. If you do not work in the defense complex of the Russian Federation or the United States, then you are unlikely to see this technology alive.
A couple more new, barely emerging technologies, used so far only by their creators, are presented below - in the section on printers.
Used metals
Ti - Titanium
Pure titanium (Ti64 or TiAl4V) is one of the most commonly used metals for 3D printing, and by far one of the most versatile as it is both strong and lightweight. It is used both in the medical industry (in personalized prosthetics) and in the aerospace and automotive industries (for the manufacture of parts and prototypes), and in other areas. The only catch is that it is highly reactive, which means it can explode easily when in powder form, and should definitely only be used for printing in an inert Argon gas environment.
SS - Stainless steel
Stainless steel is one of the most affordable metals for 3D printing. At the same time, it is very durable and can be used in a wide range of industrial and artistic applications. This type of steel alloy containing cobalt and nickel has high elasticity and tensile strength. 3D printing of stainless steel is used mainly only in heavy industry.
Inconel - Inconel
Inconel is a modern superalloy. It is manufactured by Special Metals Corporation and is a patented trademark. Consists, for the most part, of nickel and chromium, has high heat resistance. It is used in the oil, chemical and aerospace industries (for example: to create distribution nozzles, on-board "black boxes").
Al - Aluminum
Due to its inherent lightness and versatility, aluminum is a very popular metal for 3D printing applications. It is usually used in the form of various alloys, forming their basis. Aluminum powder is explosive and is used in printing in an inert Argon gas environment.
CoCr - Cobalt Chromium
This metal alloy has a very high specific strength. It is used both in dentistry - for 3D printing of dental crowns, bridges and clasp prostheses, and in other areas.
Cu - Copper
With rare exceptions, copper and its alloys - bronze, brass - are used for casting using burnt patterns, and not for direct metal printing. This is because their properties are far from ideal for industrial 3D printing applications, they are more commonly used in arts and crafts. With great success, they are added to plastic filament - for 3D printing on conventional 3D printers.
Fe - Iron
Iron and magnetic iron ore are also mainly used as an additive to PLA filament. In large-scale industry, pure iron is rarely used, and we wrote about steel above.
Au, Ag - Gold, silver and other precious metals
Most powder fusing 3D printers can work with precious metals such as gold, silver and platinum. The main task when working with them is to ensure the optimal consumption of expensive material. Precious metals are used in 3D printing of jewelry and medical products, as well as in the production of electronics.
Metal 3D printers
#1: Sciaky EBAM 300 - titanium rod
For printing really large metal structures the best choice will be EBAM from Sciaky. This device can be any size, to order. It is used primarily in the US aerospace and defense industries.
How production model, Sciaky sells the EBAM 300. It has a working area with sides of 5791 x 1219 x 1219mm.
The company claims that the EBAM 300 is one of the fastest commercially available industrial 3D printers. Structural elements of aircraft, the production of which, according to traditional technologies, could take up to six months, are now printed within 48 hours.
Sciaky's unique technology uses a high power electron beam gun to melt 3mm titanium filament, with a standard deposition rate of about 3-9 kg/h.
#2: Fabrisonic UAM - ultrasonic
Another way to 3D print large metal parts is Ultrasound Additive Manufacturing Technology (UAM) from Fabrisonic. The brainchild of Fabrisonic is a three-axis CNC machine with an additional welding head. The metal layers are first cut and then welded together using ultrasound. Fabrisonic's largest 3D printer is the “7200”, which has a build volume of 2 x 2 x 1.5 m.
#3: Laser XLine 1000 - metal powder
One of the largest metal powder 3D printers on the market has long been the Concept Laser XLine 1000. It has a build area measuring 630 x 400 x 500mm and takes up space like a small house.
The German company that made it, which is one of the suppliers of 3D printers for aerospace giants such as Airbus, recently introduced new printer- XLine 2000.
The 2000 has two lasers and an even larger build volume of 800 x 400 x 500mm. This machine, which uses patented LaserCUSING (a type of selective laser melting) technology, can create objects from alloys of steel, aluminum, nickel, titanium, precious metals, and some pure materials (titanium and bar steels.)
All major players in the metal 3D printing market have similar machines: EOS, SLM, Renishaw, Realizer and 3D Systems, as well as Shining 3D, a rapidly growing company from China.
#4: M Line Factory - Modular 3D Factory
Displacement: 398.78 x 398.78 x 424.18mm
1 to 4 lasers, 400 - 1000 watts each.
The M Line Factory concept is based on the principles of automation and interaction.
M Line Factory, from the same Concept Laser and operating on the same technology, does not focus on the size of the workspace, but on the convenience of production - it is a modular architecture apparatus that divides production into separate processes in such a way that these processes can occur simultaneously, not sequentially.
This new architecture consists of 2 independent machine units:
M Line Factory PRD (Production Unit)
The Production Unit consists of 3 types of modules: dosing module, printing module and overflow module (tray for finished products). All of them can be individually activated and do not form one continuous piece of equipment. These modules are transported through a system of tunnels inside the machine. For example, when new powder is supplied, the empty powder storage module can be automatically replaced with a new one without interrupting the printing process. Finished parts can be moved outside the machine and immediately automatically replaced by the next jobs.
M Line Factory PCG (Processing Unit - processing unit)
It is an independent data processing unit that has a built-in sieving and powder preparation station. Unpacking, preparation for the next print job and sieving take place in a closed system, without the participation of the operator.
# 5: ORLAS CREATOR - 3D printer ready to go
The creators of ORLAS CREATOR position this 3D printer as the most affordable, easy-to-use and ready-to-use, does not require the installation of any additional components and third-party programs, capable of printing directly from a complete CAD / CAM file of their own design.
All the necessary components are installed in a relatively compact case, which needs a space of 90x90x200 cm. It does not take up much space, although it looks impressive, and it weighs 350 kg.
As can be understood from the table given by the manufacturer, the metal powder is sintered by a rotating laser system, in layers 20-100 microns thick and with a “pixel” size of only 40 microns, in a nitrogen or argon atmosphere. You can connect it to a regular household power supply if your wiring can withstand a load of 10 amperes. Which, however, does not exceed the requirements of an average washing machine.
Laser power - 250 watts. The working area is a cylinder 100 mm in diameter and 110 mm in height.
#6: FormUp 350 - Powder Machine Part Method (PMPM)
The FormUp 350, powered by Powder Machine Part Method (PMPM), was created by AddUp, a joint venture between Fives and Michelin. This is the latest metal 3D printing machine, first introduced in November at Formnext2016.
The principle of operation of this 3D printer is the same as that of the above colleagues, but its main feature is different - it lies in its inclusion in PMPM.
The printer is designed specifically for industrial use, in 24/7 mode, and is designed for just such a pace of work. The PMPM system includes quality control of all components and materials at all stages of their production and distribution, which should guarantee stable high performance quality of work, in which Michelin has a huge long-term experience.
Zack Vader's MagnetoJet technology is based on the study of magnetohydrodynamics, and more specifically, the ability to control molten metal using magnetic fields. The essence of the development is that a drop of a strictly controlled size is formed from molten aluminum, and these drops are used for printing.
The size of such a droplet is from 200 to 500 microns, printing occurs at a speed of 1000 drops per second. Printer working area: 300 mm x 300 mm x 300 mm
Working material: Aluminum and its alloys (4043, 6061, 7075). And, even though it is only aluminum for now, the printer is 2 times faster than powder ones and up to 10 times cheaper.
In 2018, the Mk2 is planned to be released, it will be equipped with 10 print heads, which should give an increase in print speed by 30 times.
#9: METAL X - ADAM - atomic diffusion
Markforged presented new technology Metal 3D printing - ADAM, and a 3D printer working on this technology - Metal X.
ADAM (Atomic Diffusion Additive Manufacturing) is an atomic diffusion technology. Printing is done with metal powder, where the metal particles are coated with a synthetic binder, which is removed after printing, allowing the metal to fuse together.
The main advantage of the technology is the absence of the need to use ultra-high temperatures directly in the printing process, which means that there are no restrictions on the refractoriness of the materials used for printing. Theoretically, the printer can create 3D models from heavy-duty tool steels - now it already prints stainless steel, and titanium, Inconel and D2 and A2 steels are in development.
The technology allows you to create parts with a complex internal structure, such as in a honeycomb or in porous bone tissue, which is difficult with other 3D printing technologies, even for DMLS.
Product size: up to 250mm x 220mm x 200mm. Layer height - 50 microns.
Look, it will soon be possible to print a high-quality knife - from scratch, in a couple of hours, giving it any most intricate design.
Do you want more interesting news from the world of 3D technologies?
Metal 3D printing can be considered one of the most enticing and technologically challenging areas of additive manufacturing. Attempts to print with metals have been made since the early days of 3D printing technologies, but in most cases they ran into technological incompatibilities. In this section, we will look at technologies that have been tested for printing both composite materials containing metals and pure metals and alloys.
Inkjet 3D Printing (3DP)
Scheme of work of three-dimensional inkjet printers(3DP)Inkjet 3D printing is not only one of the oldest additive manufacturing methods, but also one of the most successful in terms of using metals as consumables. However, it is necessary to immediately clarify that this technology allows you to create only composite models due to the technological features of the process. In fact, this method allows you to create three-dimensional models from any materials that can be processed into powder. The binding of the powder is carried out using polymers. Thus, finished models cannot be called fully "metal".
At the same time, there is a possibility of converting composite models into all-metal ones due to heat treatment for the purpose of melting or burning out the binder material and sintering metal particles. The models obtained in this way do not have high strength due to porosity. An increase in strength is possible due to the impregnation of the resulting all-metal model. For example, it is possible to impregnate a steel model with bronze to obtain a stronger structure.
Models obtained in this way, even with metal impregnation, are not used as mechanical components due to their relatively low strength, but are actively used in the jewelry and souvenir industry.
Laminating Printing (LOM)
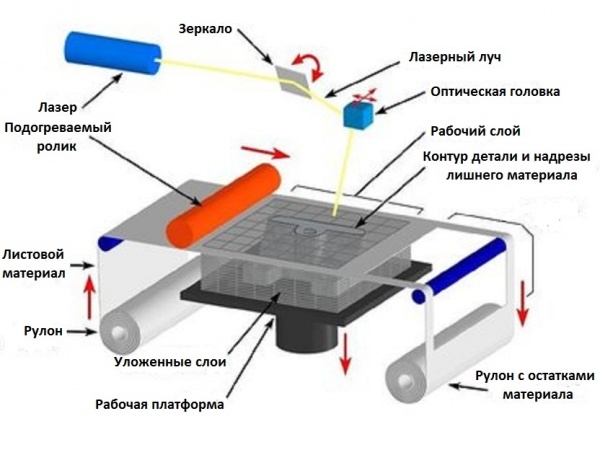
The scheme of operation of 3D printers using lamination technology (LOM)
Laminating 3D printing involves sequentially applying thin sheets of material, shaping them by mechanical or laser cutting, and then gluing them together to create a 3D model.
Metal foil can also be used as a consumable.
The resulting models are not completely metal, as their integrity is based on the use of adhesive that binds the consumable sheets.
The advantage of this technology is the relative cheapness of production and the high visual similarity of the resulting models with all-metal products. Typically, this method is used for layout.
Layered deposition (FDM/FFF)
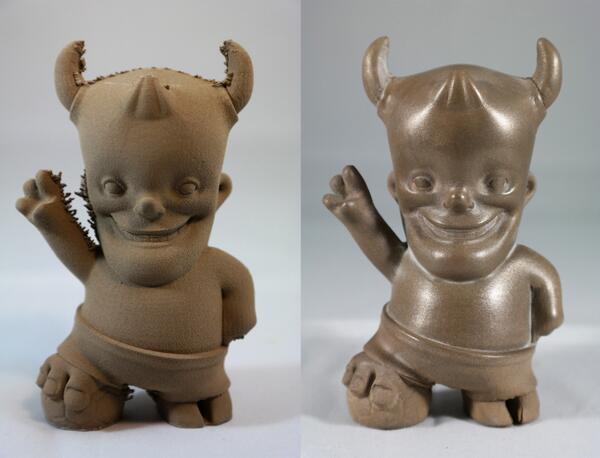
Model made with BronzeFill before and after polishing
The most popular 3D printing method has also not bypassed the attempts to use metals as consumables. Unfortunately, attempts to print with pure metals and alloys on this moment did not lead to significant success. The use of refractory metals runs into quite predictable problems with the choice of materials for the construction of extruders, which, by definition, must withstand even higher temperatures.
Printing with fusible alloys (for example, tin) is possible, but does not give enough high-quality returns for practical use.
Thus, in recent years, the attention of consumables developers has switched to composite materials, by analogy with inkjet printing. A typical example is BronzeFill, a composite material consisting of thermoplastic (details not disclosed, but apparently PLA plastic is used) and bronze powder. The resulting models have a high visual similarity with natural bronze and can even be polished to a high gloss. Unfortunately, the physical and chemical properties of finished products are limited by the parameters of the thermoplastic binder, which does not allow classifying such models as all-metal.
However, such materials may receive practical use not only in the creation of models, souvenirs and art objects, but also in industry. Thus, the experiments of enthusiasts have shown the possibility of creating conductors and shielding materials using thermoplastics with a metal filler. The development of this direction can make it possible to print electronic circuit boards.
Selective Laser Sintering (SLS) and Direct Metal Sintering (DMLS)
The most common method for creating all-metal 3D models involves the use of laser machines for sintering metal powder particles. This technology referred to as "selective laser sintering" or SLS. It should be noted that SLS is used not only for working with metals, but also with thermoplastics in powder form. In addition, metallic materials are often coated with more fusible materials to reduce the required power of laser emitters. In such cases, finished metal models require additional sintering in furnaces and impregnation to increase strength.A variation of the SLS technology is the direct metal laser sintering (DMLS) method, which, as the name implies, is focused on working with pure metal powders. These plants are often equipped with sealed working chambers filled with an inert gas for working with metals subject to oxidation, such as titanium. In addition, DMLS printers necessarily apply consumable heating to a point just below the melting point, which saves on the power of laser systems and speeds up the printing process.
The scheme of operation of SLS, DLMS and SLM installations
The laser sintering process begins with the application of a thin layer of heated powder onto a work platform. The thickness of the applied layers corresponds to the thickness of one layer of the digital model. Then the particles are sintered between themselves and with the previous layer. Changing the trajectory of the laser beam is carried out using an electromechanical system of mirrors.
Upon completion of the drawing of the layer, the excess material is not removed, but serves as a support for subsequent layers, which allows you to create models of complex shapes, including hinged elements, without the need to build additional support structures. This approach, coupled with high accuracy and resolution, makes it possible to obtain parts that require almost no machining, as well as solid parts of a level of geometric complexity that is unattainable by traditional production methods, including casting.
Laser sintering allows you to work with a wide range of metals, including steel, titanium, nickel alloys, precious materials, etc. The only drawback of the technology is the porosity of the resulting models, which limits the mechanical properties and does not allow achieving strength at the level of cast analogs.
Selective laser (SLM) and electron beam melting (EBM)
Despite high quality models obtained by laser sintering, their practical application is limited by relatively low strength due to porosity. Such products can be used for rapid prototyping, prototyping, jewelry production and many other tasks, but are of little use for the production of parts that can withstand high loads. One solution to this problem has been the conversion of direct metal laser sintering (DMLS) technology to laser melting additive manufacturing (SLM) technology. In fact, the only fundamental difference between these methods is the degree of heat treatment of the metal powder: SLM technology is based on complete melting to obtain homogeneous models that are practically indistinguishable in physical and mechanical properties from cast counterparts.
An example of a titanium implant produced using electron beam melting (EBM) technology
A parallel method that has achieved excellent results is electron beam melting (EBM). At the moment, there is only one manufacturer that creates EBM printers - the Swedish company Arcam.
EBM achieves accuracy and resolution comparable to laser melting, but has certain advantages. Thus, the use of electron guns makes it possible to get rid of the delicate electromechanical mirror systems used in laser systems. In addition, the manipulation of electron beams using electromagnetic fields is possible at speeds that are incomparably higher compared to electromechanical systems, which, coupled with an increase in power, makes it possible to achieve increased productivity without significantly complicating the design. Otherwise, the design of SLM and EBM printers is similar to laser metal sintering machines.
The ability to work with a wide range of metals and alloys allows you to create small batches of specialized metal parts that are almost as good as samples obtained using traditional production methods. There is no need to create additional tools and infrastructure such as molds and furnaces. Accordingly, significant savings are possible in prototyping or small-scale production.
Laser and electron beam melting plants have been successfully used to produce items such as orthopedic titanium prostheses, gas turbine blades and jet engine injectors, among others.
Direct laser additive construction (CLAD)
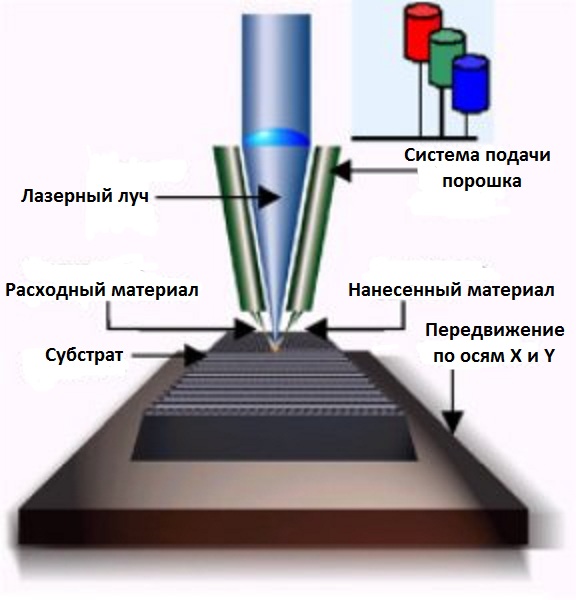
Scheme of operation of plants using CLAD technology
Not so much 3D printing technology, but "3D repair" technology. The technology is used exclusively at the industrial level due to the complexity and relatively narrow specialization.
CLAD is based on the deposition of metal powder on damaged parts with immediate surfacing using a laser. Positioning print head» carried out along five axes: in addition to movement in three planes, the head has the ability to change the angle of inclination and rotate around the vertical axis, which allows you to work at any angle.
Such devices are often used to repair large-sized products, including manufacturing defects. For example, the installations of the French company BeAM are used to repair aircraft engines and other complex mechanisms.
Complete CLAD units use a sealed, inert atmosphere working chamber to handle titanium and other oxidizable metals and alloys.
Arbitrary electron beam melting (EBFȝ)
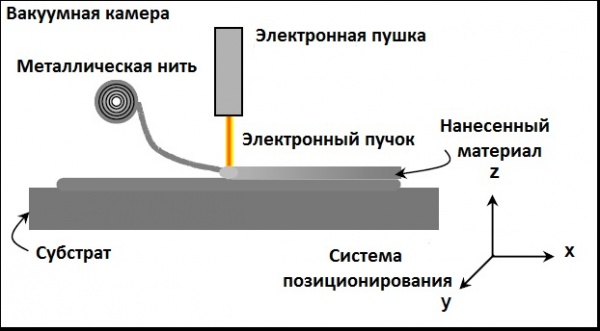
Scheme of operation of EBFȝ printers
A technology developed by NASA for use in zero gravity. Since the absence of gravity makes working with metal powders almost impossible, EBFȝ technology involves the use of metal threads.
The construction process is similar to Fused Deposition 3D printing (FDM), but using an electron beam gun to fuse the consumable.
This technology will allow the creation of metal spare parts in orbit, which will significantly reduce the cost of delivering parts and provide the ability to quickly respond to emergency situations.
Metal powders are the most durable material for 3D printing. Products created on metal 3D printers are superior in many respects to analogues produced using traditional technologies (casting, rolling, etc.).
Main characteristics of metal powder products
- Increased strength
- Any geometry
- Large selection of metals and their alloys
- Rough surfaces
- No metal tension
- Any post-processing
- Support material used for reprinting
Metal 3D printing technologies
Selective Laser Melting (SLM)- selective fusion of powder material using a laser, the most popular metal 3D printing technology. Used in metal 3D printers by SLM Solutions and Realizer. Read more about SLM technology.
Direct Metal Printing (DMP)- an analogue of SLM technology used in 3D Systems ProX series 3D machines.
Electron Beam Melting (EBM)- sintering of metal powders under the influence of an electron beam gun. Used in Arcam 3D printers.
Types of metal powders for 3D printing
Titanium. High-strength biocompatible material used in medicine, aircraft construction, mechanical engineering, and industry. .
Tool and stainless steel. Various steel alloys are the most common materials for 3D printing. They serve to solve a wide range of tasks in various fields, are resistant to corrosion, have increased strength and wear resistance. .
Aluminum and its alloys. A light alloy that has a lower density than other 3D printing metals. It has good alloying properties and electrical conductivity. Used in automotive, aerospace, industry. .
Cobalt chrome. Corrosion resistant biocompatible material. It has high strength, is used in medicine and dentistry, as well as industries with high temperatures.
The latest technologies and devices no longer cause much enthusiasm for anyone; every year something new and original appears on the market. The same thing happened with 3D printers. There are many varieties of it, each of them works with different materials. But entrepreneurs, and people who are going to organize their production, were interested in a 3D printer working on metal.
This new handy device can be a great choice for organizing your business. Having bought a small home model, you can start the production of single orders, and then turn around and go to a larger production. But let's talk about everything in order.
Varieties of printers
State-of-the-art 3D printers are able to create with materials of different textures. But recently, most of the devices are based on work in which the consumable raw material is metal in the form of a powder. A 3D printer that prints only metal is divided into three main types:
- Jet. He creates prototypes from metals such as lead or tin.
- Three-dimensional, which works on the basis of metal powder, with the effect of gluing. Such devices print a prototype, which then needs to be fired, but the products created by it do not have good quality properties.
- Metal laser 3D printer. These parts are most often used in large-scale enterprises, and their price is rather big.
Each of the described models has its pros and cons, but the laser is still considered the best.. It is currently possible to purchase a model that produces prototypes excellent quality and in small quantities. The table below lists a few printers that produce good quality products.
With any of the options described above, you can start your own business. Those models that are cheaper do not differ in the quality of products from expensive ones. Each model prints with metal, and it is used in several technologies.
Types of technologies for 3D printing
Each of the existing technologies is good in its own way. Which one to choose to start your own business in order to start a sharp start and make money on a good 3D printer in a short time? The table below describes all processes where the metal is used in powder form.
Technology name | Principle of operation |
SLS | Translated means selective sintering with a laser, during this process a minimum amount of products can be created. |
SLM | This technology means the selective direction of metal particles by means of a laser, they are melted and welded, after which a very rigid base is obtained. This process is carried out in a vacuum chamber filled with gas inside. |
EBM | And this technology means electron beam melting of metal powder, under the influence of electron beams it melts. With the help of this technology, models are produced that are used in medicine, the aerospace industry and in the construction of cars. |
Now it’s worth taking a closer look at each technology in more detail in order to determine exactly what a home 3D printer that prints on metal should be. Each technology has its pros, but it also has its cons. Only by understanding each of them, you can make a rational choice that will allow you to purchase a good and easy-to-use model with a small budget.
SLS. Selective laser sintering is based on high power laser emitters. During operation, all metal particles are sintered, and the result is a 3D prototype. But also sintering can be carried out without the use of components that help the bond. The prototype is made in layers: first, it is immersed in a photopolymer resin, then powder is applied, and the computer indicates which places should be treated with a laser beam.
During printing, screenings remain as a powder, they can be used in the future as a supporting surface for creating other models. This approach will reduce the cost of printing. But this technology also has a minus - the structure of the products is porous, therefore, it requires further processing, during which the density will be increased.
A cheap sPro 140 or sPro 230 metal 3D printer is a great choice for starting a business. These two models create SLS prints and are able to make even miniature details, and they will be perfectly detailed. Also during the press on them, all materials are spent economically.
SLM. This technology involves melting with a metal powder, under the influence of a laser beam. The platform on which the material is applied slowly lowers, thus forming the layers of the 3D part. If you choose a printer from this model, then Pro will be the best choice. X100 is a mini model. It can be used to create chemically pure metal and ceramic prototypes.
A printer that prints using this technology is not cheap, but at the same time it is able to create very good and high-quality models, it will be an excellent choice in case of business expansion, but it is expensive to start a business.